How to win customers and influence the(ir On Time Delivery) improvement… through reliable world class supply chain performance.
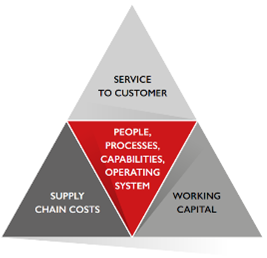
In this 2-part blog series we will ask and address the 4 Killer Questions to measure and improve your OTD On Time Delivery that every Supply Chain leader should ask, but some are still are afraid to..
Put the Focus on Execution Reliability (first) let the Fortune Telling (Demand Predictability) come later..
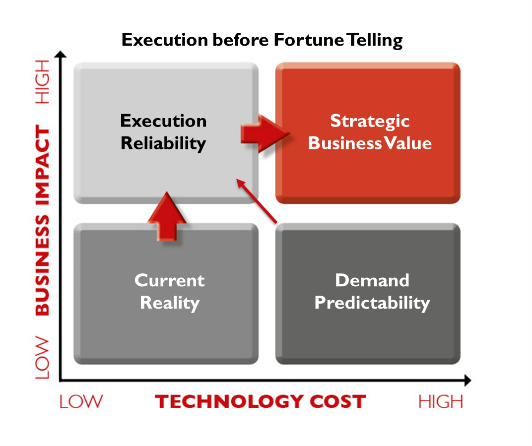
Many Supply Chain leaders fall into the trap of striving to achieve flawless forecast accuracy with the perpetual investment in untold iterations of new technology, along with a continual re-invigoration the old, energy sapping under-achieving S&OP processes. Perhaps you will kick off IBP process, re-grouping product families or re-organising commercial supply chain teams or gamble all on the silver bullet of applied Machine Learning.
Then, once flawless forecast accuracy is still not achieved and if all else fails then the application of some creative leadership to “Optimise” the definition of “OTD – On Time Delivery” may get you to where you think your customers want you to be (you know, lets measure to promise, lets put a 1 day tolerance on our delivery target, talk about the average over an entire month)…….Shifting out of this paradoxical situation on a daily basis and putting the emphasis on Execution Reliability vs Demand Predictability is tough, but it is key in shifting towards world class performance – You do not get to world class without putting the hard yards into execution reliability first >> Move up the axis of execution reliability, then, and only then put the investment into Technology to increase Demand Predictability, this approach will no doubt enable world class on time delivery performance, business growth and your competitive advantage.
In this 2-part blog series we will explore the role you will need, and the 4 killer questions you should ask of your Supply Chain every day to measure and improve your OTD performance.
Killer Question No. 1
How well did we serve our customers yesterday, and how successfully did we p**s them off?
Check your OTD On Time-Delivery Performance – every day, for every customer, for every order. Calculate your Outside-In™ Span metric.
Irrespective of whether your OTD performance is measured to the Minute, Hour or Day – create the view where you get to see the performance (and variation) of every order, every day.
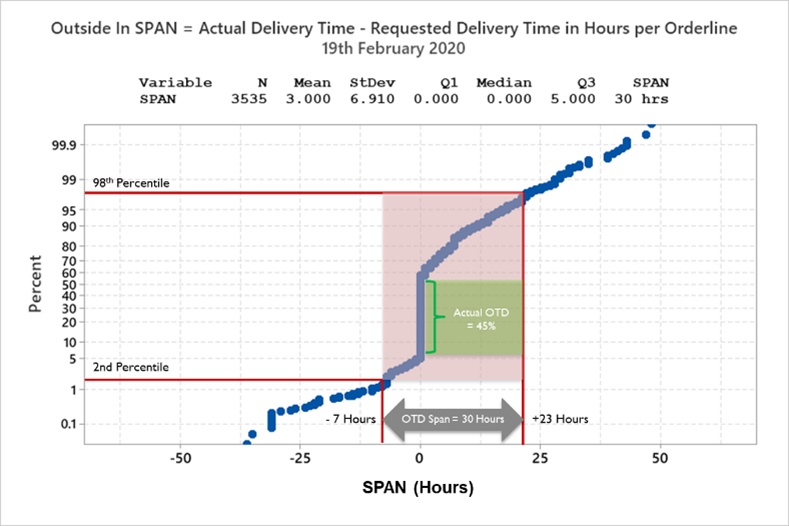
Plot the Span:
For every order, every customer, from every DC.
Actual Delivery Time – Requested Delivery Time
= Δ Minutes / Hours / Days
The calculated SPAN is the difference between 2ndPercentile and 98th Percentile. Expressed in hours. In the case shown the span is 30 Hours >> The role of EVERY Supply Chain leader is to know their Span and improve it.
Taking this approach to understand your OTD On-Time Delivery SPAN performance at Order Line level will give you the visibility to help everybody in the Supply Organization see, and understand why underperformance & variability in your performance exists. You will provide the opportunity to see and learn to your whole supply chain organisation.
Killer Question No. 2
What do we really do, how is my Supply Chain really connected and what s**t do I need to fix?
How does my process truly operate, day to day, what keeps my Supply Chain linked and how do I make sure it steps forward stepping together?

The management, maintenance of and adherence to an effective Supply Chain operating system will bring you 1 step closer to reducing your overall OTD SPAN. Clearly every organisation is different and the list is not exhaustive but to really impact SPAN a good grasp of how you are performing across the following dimensions is required….
- Supply Chain Operating Rules and Standard Operating Procedures Simple, but often overlooked and their impact on performance often understated. How do your people, across each line of business, within each geographic region, within each department know how to act and react given the different necessary and complex functions of any supply chain team – and if the knowledge is there, then how well do your teams really stick to the game plan?
- Inputs, Outputs and Functional Handoffs for each link in the chain
As any student of Process Mapping / Swimlane diagrams will attest to, 90% of process failures / errors / defects occur at the point of handoff from one team or department to another (electronic or not) – are these standards and expectations set along your supply chain and how well are they adhered to? - Master Data Management
Master Data Management (MDM) becomes increasingly important with the onset of Digitisation – any supply chain is built on a solid foundation of Master Data across Bills of Materials & Supply Chain Parameters such as Leadtime’s & Quantities from Customer Master Data to Logistics requirements – Any weakness in MDM will result in Supply Chain cost, capital or service issues. - Touchpoints along the Chain
Touches are ‘gold’ for Supply Chain improvement – they uncover the weaknesses in 1, 2 & 3 above…..treat them well, welcome them, get to know them. And just stop them.
Killer Questions 3 & 4 will be in the next part of this blog. In the meantime, if you would like to know more, easily schedule a call or read more about OTD Performance and our methodologies Stable Supply Chain and Data Driven Leadership.
Keith Bestwick is Partner at R&G Global Consultants, located in United Kingdom.